24 septembre 2014
3
24
/09
/septembre
/2014
03:28
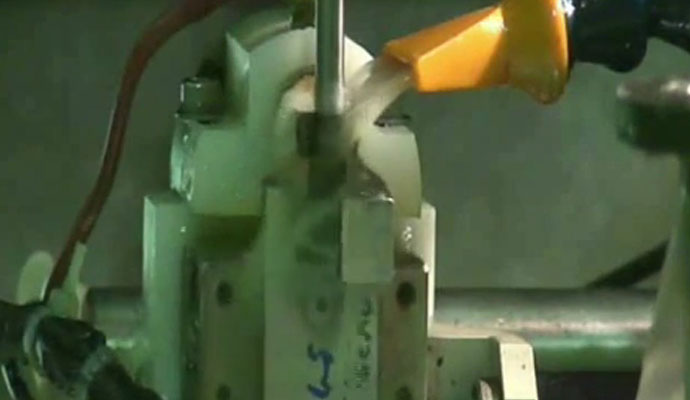
固定磨粒方式拋光加工

微粒磨輪研磨法
粒磨輪研磨法使用結合劑較差的微細磨粒磨輪的搪光或超精加工,主要是作為圓筒狀機械零件的內外圓周面之精加工方法,自古以來就已實用化了。
軟質結合磨輪研磨法
軟質結合磨輪研磨法使用容易彈性變形的軟質結合劑,使磨粒前端的接觸壓力均勻的方法。使用低結合度容易脫落的結合劑,防止堵屑的方法。將微細磨粒黏到柔軟性高的膠帶狀或薄板狀的基材上,目標鎖定作用壓力均勻化的方法等。
軟質磨粒磨輪研磨法
軟質磨粒磨輪研磨法使用以低結合度結合劑,固定將具有機械化學效果的軟質磨粒之MCP磨輪,進行研磨的MCP磨輪拋光,脫落的磨粒是以游離磨粒來作用,而提高研磨效率。具有固定磨粒方式,且又容易得到無變形、超平滑表面的特徵。
薄膜研磨
研磨用薄膜分為被覆型與一體成形型。但主體為被覆型,利用靜電塗裝法或羅拉被覆法,一般是將單層或數層的磨輪磨粒層,均勻塗上聚酯薄膜。由於其薄且柔軟的特性,可因應平面、圓筒面或自由形狀,為其優點。使用磨粒的粒徑為0.1〜60μm左右,磨金屬材料使用氧化鋁或碳化矽,磨硬脆材料則使用鑽石磨粒。
機械化學拋光MCP
機械化學拋光是使用較加工物軟且與加工物會產生固相化學反應的磨粒,在加工物與磨料之間,由於力學作用產生機化反應,在表面形成的反應物以機械方式去除。
超聲波拋光
超聲波拋光將工件放入磨料懸浮液中並一起置於超聲波場中,依靠超聲波的振盪作用,使磨料在工件表面磨削拋光。超聲波加工宏觀力小,不會引起工件變形,但工裝製作和安裝較困難。超聲波加工可以與化學或電化學方法結合。在溶液腐蝕、電解的基礎上,再施加超聲波振動攪拌溶液,使工件表面溶解產物脫離,表面附近的腐蝕或電解質均勻;超聲波在液體中的空化作用還能夠抑制腐蝕過程,利於表面光亮化。
ELID研磨法
ELID研磨法是使用金屬結合劑磨輪的研磨,利用供給弱導電性研磨液,使磨輪表面的結合劑材料稍微溶解,可防止磨輪填塞,以持續穩定的研磨。
EPD研磨法
利用與負極帶電的高分子電解質混合的超微粒(10~2Onm的二氧化矽粉等),電氣游動現象使用凝聚於電極的直徑10mm左右晶片狀磨輪,進行研磨。這種磨輪的結合度很差,故很容易就磨耗了。不加研磨液,利用脫落磨粒的游離磨粒拋光法,實施起來很適當。
資料來源:網路彙整
willy
6 août 2014
3
06
/08
/août
/2014
08:01

游離磨粒方式拋光加工

機械拋光
在游離磨粒方式中,為最普遍且基本的研磨方法,機械拋光是靠切削、材料表面塑性變形去掉被拋光後的凸部而得到平滑面的拋光方法,一般使用油石條、羊毛輪、砂紙等,以手工操作為主,特殊零件如回轉體表面,可使用轉檯等輔助工具,表面品質要求高的可採用超精研拋的方法。超精研拋光是採用特製的磨具,通常將lμm以下的硬質微細磨粒與加工液混合的研磨液,緊壓在工件被加工表面上,作高速旋轉運動,一面供給到旋轉的碟狀平板,一面以一定壓力壓在加工物上研磨的接觸式拋光。利用該技術可以達到 Ra0.008μ m 的表面粗糙度,是光學玻璃(鏡片、窗戶等)、硬質金屬(精密模具或磁碟基板等)、陶瓷(構造用機構零件、電子用基板等)的高精度研磨的技術。
化學機械式研磨法CMP
化學機械式拋光為研磨液的化學腐蝕作用與磨粒的機械式切削作用之複合方法。去除表面生成物拋光是因研磨液的作用,而以磨粒的切削作用,去除在加工物表面產生摻水膜或氧化膜等之拋光方法。
電/磁研磨拋光
電場和磁場拋光加工是利用和控制電、磁場的強弱使磁流體帶動磨粒對工件施加壓力從而對高形狀精度、高表面品質和晶體無畸變的表面進行加工的拋光方法。主要用於資訊設備和精密機械高性能元件的加工。採用合適的磨料,表面粗糙度可以達到 Ra0.1μ m 。
浮动抛光
浮動拋光(Float Polishing)使用高平面度平面並帶有同心圓或螺旋溝槽的錫拋光盤,使拋光盤及工件高速回轉,在二者之間拋光液呈動壓流體狀態,形成一層液膜,從而使工件在浮起狀態下進行拋光。
非接觸研磨拋光
非接觸研磨技術是以彈性發射加工(EEM)的理論為基礎的。
彈性發射加工(EEM)
EEM方法是利用微細粒子在材料表面上滑動時去除材料的加工。微細粒子以接近水準的角度與材料碰撞,在接近材料表面處產生最大的剪斷應力,既不使基體內的位錯、缺陷等發生移動(塑性變形),又能產生微量的“彈性破壞”,以進行去除加工。原理上是採用噴射粒子的加工方式,要儘量以小角度撞擊加工表面,其加工精度接近於原子級,加工單位為0.1 μm以下,可獲得相當好的表面。加工時研具於工件不接觸,使微細粒子在研具與工件表面之間自由狀態流動,當使微細粒子撞擊工件表面時,則產生彈性破壞物質的原子結合,從而獲得無干擾的加工表面。加工方法是使用聚氨酯球作加工頭,在微細粒子混合均勻的懸浮液中,使加工頭邊回轉邊向工件表面靠近,是混合液中的微細粒子在工件表面的微小面積(Φ1~2mm)內產生作用,進行加工。
資料來源:網路彙整
willy
25 juillet 2014
5
25
/07
/juillet
/2014
03:22

拋光加工原理
利用柔性拋光工具和磨料顆粒或其他拋光介質對工件表面進行的修飾加工。拋光不能提高工件的尺寸精度或幾何形狀精度,而是以得到光滑表面或鏡面光澤為目的,有時也用以消除光澤(消光)。通常以拋光輪作為拋光工具。拋光輪一般用多層帆布、毛氈或皮革疊制而成,兩側用金屬圓板夾緊,其輪緣塗敷由微粉磨料和油脂等均勻混合而成的拋光劑。拋光時,高速旋轉的拋光輪(圓周速度在20米/秒以上)壓向工件,使磨料對工件表面產生滾壓和微量切削,拋光的去除單位很小,故加工效率低,且因為使用容易變形的拋光機,故為容易產生形狀崩潰的工程。所以在施工上儘可能以較少的去除量,獲得光亮的加工表面,表面粗糙度一般可達Ra0.63~0.01微米;當採用非油脂性的消光拋光劑時,可對光亮表面消光以改善外觀。
拋光加工效率的因素
- 拋光加工量 R=k.p.v.t 其中p為拋光壓力、v為拋光速度、t為加工時間、k為比例常數。
- 拋光效率與附加壓力(p)及拋光距離(v.t)成正比。
- 為了保持一定的加工效率,除了拋光壓力、速度等加工條件外,嚴加管理研磨液濃度、溫度、拋光機的狀態等,是使拋光穩定的重要因素。
研磨的加工變質層
- 加工變質層使工件材質的結構、組織和組成遭到破壞或接近於破壞狀態。在變質層部分存在變形和應力,還有其物理的和化學的影響等。硬度和表面強度變化等機械性質和耐腐蝕性等化學性質也與基體材料不同。
- 硬脆材料經研磨後的表面 ,經研磨的單晶矽表面,使用氟、硝酸系列的溶液進行化學浸蝕,依次去掉表層,用電子衍射法進行晶體觀察時,從表層向內部的順序為非晶體層或多晶體層、鑲嵌結構層、畸變層和完全結晶結構。另外,從使用X射線衍射法的彈塑性學的觀點來評價,則表層是由極小的塑性流動層構成,其下是有異物混人的裂紋層,再下則是裂紋層、彈性變形層和主體材料。
- 在研磨金屬材料時,雖不發生破碎,但磨粒轉動和刮削時,由於材料承受了塑性變形,通常形成與上述矽片相類似的加工變質層。相反,例如是多晶的金屬材料,則越接近被加工的表層,晶粒越微細,累積位錯在最表層,變成非晶質狀態。在這部分,金屬與大氣中的活性氧結合,變得活躍。另外,有時發生因塑性變形而使磨粒等容易嵌進金屬。
資料來源:網路彙整
willy
11 juin 2014
3
11
/06
/juin
/2014
04:08
航空難加工材料強度大、硬度高,耐衝擊、加工中容易硬化,切削溫度高、刀具磨損嚴重,如鎳基高溫合金、鈦合金、高強度結構鋼碳纖複合材等被現代航空產品大量採用。
航空難加工材料加工最突出問題是刀具磨損問題及鑽孔毛邊、撕裂情形,直接影響加工效率和成本;此外加工質量也經常成為瓶頸。目前碧威(股)公司針對航太金屬及複合材料鑽孔加工刀具開發,特殊刀口幾何與多複合材質鑽孔加工應對上均有卓越效果。(此報告針對航空難加工材料的鋁合金、銅網碳纖複合材及碳纖材質測試鑽孔)
鋁合金材料鑽孔測試
BW公司開發多角鑽頭使用氣動工具/鑽孔機直接進行鉸孔,工件為航太用高階鋁合金板,進行穿透鑽孔。
鑽孔加工條 |
航太用高階鋁合金板 |
加工件 |
厚度3mm 航太用鋁合金板 |
 |
加工刀具 |
BW複合材專用多角鑽頭 |
加工機台 |
氣動工具/鑽孔機 |
加工方式 |
鑽孔,無任何切削油、水與無冷風處理 |
加工條件 |
主軸轉速:6000rpm 加工後用標準孔位公差棒測試,孔位以達到正確公差。 |
銅網碳纖複合材料鑽孔測試
BW公司開發多角鑽頭使用氣動工具/鑽孔機直接進行鉸孔,工件為航太用銅網碳纖複合材料板,進行穿透鑽孔。
鑽孔加工條件 |
銅網碳纖複合材料 |
加工件 |
厚度3mm航太用銅網碳纖複合 |
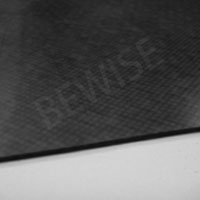 |
加工刀具 |
BW複合材專用多角鑽頭 |
加工機台 |
氣動工具/鑽孔機 |
加工方式 |
鑽孔,無任何切削油、水與無冷風處理 |
加工條件 |
主軸轉速:6000rpm 加工後用標準孔位公差棒測試,孔位以達到正確公差。 |
碳纖維複合材鑽孔測試
BW公司開發多角鑽頭使用氣動工具/鑽孔機直接進行鉸孔,工件為航太用銅碳纖維複合材,進行穿透鑽孔。
鑽孔加工條件 |
碳纖維複合材 |
加工件 |
厚度5mm航太用碳纖維複合材 |
< |
加工刀具 |
BW複合材專用多角鑽頭 |
加工機台 |
氣動工具/鑽孔機 |
加工方式 |
鑽孔,無任何切削油、水與無冷風處理 |
加工條件 |
主軸轉速:6000rpm 加工後用標準孔位公差棒測試,孔位以達到正確公差。 |
Voir les commentaires
willy
12 mai 2014
1
12
/05
/mai
/2014
05:15
willy
21 avril 2014
1
21
/04
/avril
/2014
02:57

表面粗糙度
表面粗糙度是指工件表面上具有的較小間距的微小峰谷組成的微觀幾何形狀特性。表面缺陷應從中排除,且不考慮表面其他物理特性諸因素;為避免與光亮,清潔的概念混淆並與國際間稱呼一致,不採用“表面光潔度”這一術語,而稱作表面粗糙度。
切削加工與表面粗糙度
表面粗糙度是在機械加工過程中,由於刀痕,材料的塑性變形,機械加工高頻振動,刀具與被加工表面的摩擦等原因引起的。它對零件的配合性能,耐磨性,抗腐蝕性,接觸剛度,抗疲勞強度,密封性和外觀等都有影響。
同一零件上,工作表面的粗糙度允許值應小於非工作面的表面粗糙度允許值,配合性質相同時,零件尺寸小的比尺寸大的表面粗糙度允許值要小;同一公差等級,軸比孔的表面粗糙度允許值要小;運動速度高,壓力大的摩擦表面比運動速度低,壓力小的摩擦表面粗糙度允許值小;一般來講,表面形狀精度要求高的表面,表面粗糙度允許值也小;不同的表面粗糙度允許值,其加工方法是不同的,因此,經濟效果也是不同的,在選擇表面粗糙度允許值時必須予以考慮。
影響切削加工表面粗糙度的常見因素
刀具幾何形狀及切削運動的影響
刀具相對於工件作進給運動時,在加工表面留下了切削層殘留面積,從而產生了表面粗糙度,殘留面積的形狀是刀具幾何形狀的複映,其高度受刀具的幾何角度和切削用量大小的影響。
工件材料性質的影響
加工塑性材料時,由於刀具對加工表面的擠壓和摩擦,使之產生較大的塑性變形,加之刀具迫使切屑與工件分離時的撕裂作用,使表面粗糙度值加大。一般來說,材料塑性變形趨勢越大或韌性越大,被加工表面粗糙度就越大。切削脆性材料時,塑性變形小些,控制好切屑崩碎現象,就容易達到表面粗糙度的要求。對於同樣的材料。金相組織越是粗大,切削加工後的表面粗糙度值也會越大。
切削用量
切削用量中,切削速度對表面粗糙度的影響比較複雜。但在中等速度下,塑性材料由於容易產生積屑瘤與鱗刺,且塑性變形較大,因此表面粗糙度值會變大。加工脆性材料時,由於塑性變形很小,主要形成崩碎切屑,切削速度的變化對表面粗糙度影響較小。減少進給量f可以減少切削殘留面積高度,使表面粗糙度值減小。但進給量f太小刀刃不能切削而形成擠壓,增大了工件的塑性變形,反而會增大表面粗糙度值。一般,背吃刀量對表現粗糙度影響不明顯。
振動
無論外界振動的傳入,機床內部運動部件的振動,還是機械系統在某特定條件下產生的切削振動均會嚴重惡化工件表面粗糙度,所以必須採取適當的措施來減少振動。
高溫切削產生切削熱
在高速切削條件下,高溫效應導致工件已加工淺薄表面發生熔融現象,在刀具運動的作用下, 工件已加工淺薄表面熔融金屬發生少量定向粘塑形流動。
積屑瘤的影響
在切削過程中,當刀具前刀面上存在積屑瘤時,由於積屑瘤的頂部很不穩定,容易破裂,一部分連附於切屑低部而排出,一部分則殘留在加工表面上,使表面粗糙度增大。
鱗刺
鱗刺是指已加工表面上鱗片狀的毛刺,是用高速鋼刀具低速切削時,經常見到的一種現象。鱗刺一般是在積屑瘤增長階段的前期裡形成的。甚至在沒有積屑瘤的時候,以及在更低一些的切削速度範圍內也有鱗刺發生。
資料來源:網路彙整
willy
19 mars 2014
3
19
/03
/mars
/2014
01:57
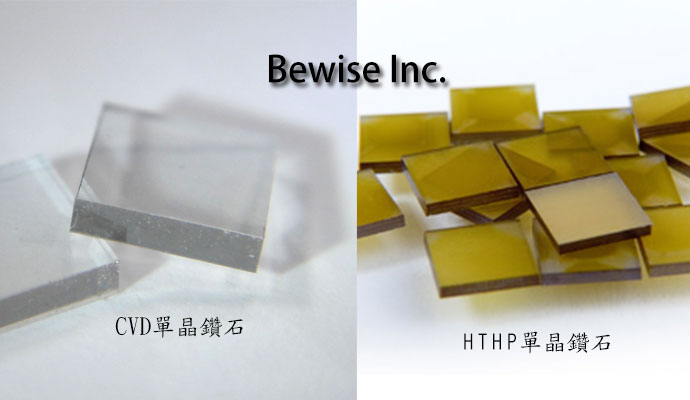
鑽石在任何大批量材料中具有最高的硬度和導熱係數,並且以其卓越的光學特性,電學性能,化學以及抗磨損性能,使得鑽石成為在科學和工業領域中最廣受歡迎的材料。

平面和取向是由叫做米勒指數的標號系統表示。鑽石的許多屬性都是依賴于取向。鑽石的硬度和拉伸強度變化在不同的方向上都有所差異。它還有一個完美的八面體裂解面,沿裂解面可以容易地分割並留下一個光滑的表面。鑽石定向偏差是由於不同取向的原子之間的結合強度的差異。
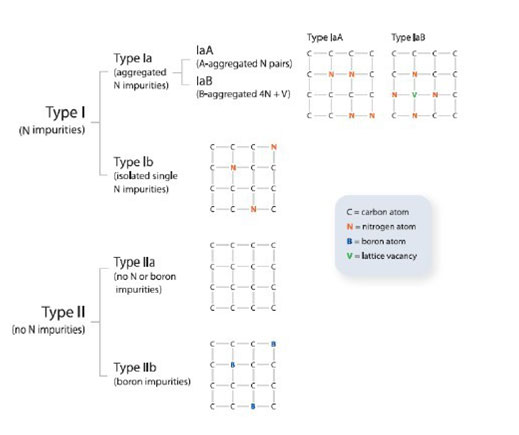
鑽石科學的分為4種類型,類型ⅠA,類型ⅠB,類型ⅡA,類型ⅡB,由雜質的數量級別和類型來區分,並以原子尺度的方式測量。而Ⅱa型鑽石具有最高的純度,它們是最接近理想完美晶體。因此,Ⅱa型鑽石無疑是實驗室培育出最好的鑽石近似乎天然鑽石一樣。市場上現有的大多數鑽石是HTHP鑽石(高溫高壓)和聚晶鑽石(PCD)。HTHP鑽石屬於類型ⅠB,它是暗黃色高濃度的氮雜質,主要用於工業磨料,表面修整和其他一些機械部件。
CVDD與天然鑽石機械性能:
性能 |
天然鑽石 |
CVD單晶鑽石 |
硬度(kgf/mm2) |
>8000 |
>8000 |
密度(g/cm3) |
3.52 |
3.52 |
楊氏模量(GPa) |
>1200 |
>1000 |
斷裂性(J/M) |
10 |
25 |
摩擦係數(相對於鋼) |
0.1 |
0.1 |
熱導率(W/cm·K) |
25 |
>20 |
磨耗比 (111方向) |
>40×104 |
>30×104 |
電阻率(Ω·cm) |
不導電 |
1014~1016 |
化學惰性 |
常溫下不溶於所有酸和鹼 |
常溫下不溶於所有酸和鹼 |
CVDD與PCD刀具比較:
CVDD刀具刀刃強度高,具有接近于單晶金剛石刀具的抗衝擊性能,能製作具有各種尺寸的刀具; CVDD刀具耐磨性好,耐用度比硬質合金高100 倍以上;用單晶金剛石刀具的研磨方法將刃部精細研磨拋光至Ra0.05 µm以下,工件表面可達到鏡面;熱導率5~10W/cm•K在幹切過程中,可將刀尖的熱量及時擴散,減少對工件表面損傷,降低刀具使用溫度以及提高刀具壽命。
性能 |
PCD |
CVD單晶鑽石 |
材質結構 |
含Co粘結劑 |
純鑽石 |
耐磨性 |
隨金剛石顆粒大小而變 |
高於PCD2~10倍 |
韌性(抗衝擊性) |
較好 |
略差 |
耐溫性 |
低於500℃ |
高於700℃ |
熱導率 |
熱導率低 |
熱導率高 |
化學穩定性 |
低 |
高 |
適用性 |
濕切-不適於加工有機複合材料 精加、半精加、連續切削 |
濕切、乾切-適於加工有機複合材料粗加工、精加工 |
資料來源:網路彙整
willy
12 février 2014
3
12
/02
/février
/2014
02:45
willy
24 janvier 2014
5
24
/01
/janvier
/2014
03:41
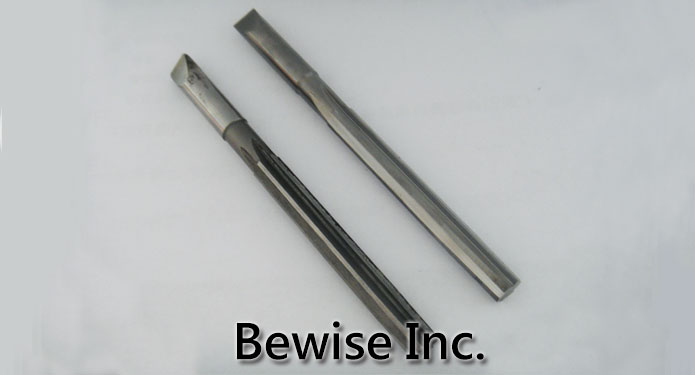
鉸孔是將擴大一個已經存在的孔。鉸孔和鑽孔、擴孔一樣都是由刀具本身的尺寸來保證被加工孔的尺寸的,但鉸孔的品質要高得多。鉸孔時,鉸刀從工件孔壁上切除微量金屬層,以提高其尺寸精度和減小其表面粗糙度值,鉸孔是孔的精加工方法之一,常用作直徑不很大、硬度不太高的工件孔的精加工,也可用于磨孔或研孔前的預加工。鉸孔多以鉸刀做加工刀具,鉸刀是用於孔的精加工和半精加工的刀具,加工餘量一般很小。鉸刀可用手動或裝在鑽床、車床、搪床等主軸上使用,在鉸削過程中,一般多為鉸刀一方面旋轉,一方面沿著軸向進給。鉸削生成的切屑量很小,故其切屑排出溝槽亦比鑽頭小。機鉸生產率高,勞動強度小,適宜于大批大量生產。
在鉸孔加工過程中,經常出現孔徑超差、內孔表面粗糙度值高等諸多問題。
鉸孔常見問題/解決方案
鉸孔常見問題 |
問題產生的原因 |
解決措施 |
孔徑增大,誤差大 |
(1)鉸刀外徑尺寸設計值偏大或鉸刀刃口有毛剌 (2)切削速度過高 (3)進給量不當或加工餘量太大(4)鉸刀主偏角過大(5)鉸刀彎曲 (6)鉸刀刃口上粘附著切屑瘤 (7)刃磨時鉸刀刃口擺差超差 (8)切削液選擇不合適 (9)安裝鉸刀時,錐柄表面油污未擦乾淨,或錐面有磕、碰傷 (10)錐柄的扁尾偏位,裝入機床主軸後與錐柄圓錐干涉 (11)主軸彎曲或主軸軸承過松或損壞 (12)鉸刀浮動不靈活,與工件不同軸 (13)手鉸孔時兩手用力不均勻,使鉸刀左右晃動 |
根據具體情況適當減小鉸刀外徑;降低切削速度;適當調整進給量或減少加工餘量;適當減小主偏角;校直或報廢彎曲的不能用的鉸刀;用油石仔細修整到合格;控制擺差在允許的範圍內;選擇冷卻性能較好的切削液;安裝鉸刀前必須將鉸刀錐柄及機床主軸錐孔內部油污擦淨,錐面有磕碰處用油石修光;修磨鉸刀扁尾;調整或更換主軸軸承;重新調整浮動卡頭,並調整同軸度;注意正確操作。 |
孔徑縮小 |
鉸刀外徑尺寸設計值偏小;切削速度過低;進給量過大;鉸刀主偏角過小;切削液選擇不合適;刃磨時鉸刀磨損部分未磨掉,彈性恢復使孔徑縮小;鉸鋼件時,餘量太大或鉸刀不鋒利,易產生彈性恢復,使孔徑縮小;內孔不圓,孔徑不合格。 |
更換鉸刀外徑尺寸;適當提高切削速度;適當降低進給量;適當增大主偏角;選擇潤滑性能好的油性切削液;定期互換鉸刀,正確刃磨鉸刀切削部分;設計鉸刀尺寸時,應考慮上述因素,或根據實際情況取值;作試驗性切削,取合適餘量,將鉸刀磨鋒利。 |
鉸出的內孔不圓 |
鉸刀過長,剛性不足,鉸削時產生振動;鉸刀主偏角過小;鉸刀刃帶窄;鉸孔餘量偏;內孔表面有缺口、交叉孔;孔表面有砂眼、氣孔;主軸軸承鬆動,無導向套,或鉸刀與導向套配合間隙過大;由於薄壁工件裝夾過緊,卸下後工件變形。
|
剛性不足的鉸刀可採用不等分齒距的鉸刀,鉸刀的安裝應採用剛性聯接,增大主偏角;選用合格鉸刀,控制預加工工序的孔位置公差;採用不等齒距鉸刀,採用較長、較精密的導向套;選用合格毛坯;採用等齒距鉸刀鉸削較精密的孔時,應對機床主軸間隙進行調整,導向套的配合間隙應要求較高;採用恰當的夾緊方法,減小夾緊力。 |
孔的內表面有明顯的棱面 |
鉸孔餘量過大;鉸刀切削部分後角過大;鉸刀刃帶過寬;工件表面有氣孔、砂眼;主軸擺差過大。
|
減小鉸孔餘量;減小切削部分後角;修磨刃帶寬度;選擇合格毛坯;調整機床主軸。 |
內孔表面粗糙度值高 |
切削速度過高;切削液選擇不合適;鉸刀主偏角過大,鉸刀刃口不在同一圓周上;鉸孔餘量太大;鉸孔餘量不均勻或太小,局部表面未鉸到;鉸刀切削部分擺差超差、刃口不鋒利,表面粗糙;鉸刀刃帶過寬;鉸孔時排屑不暢;鉸刀過度磨損;鉸刀碰傷,刃口留有毛刺或崩刃;刃口有積屑瘤;由於材料關係,不適用於零度前角或負前角鉸刀。
|
降低切削速度;根據加工材料選擇切削液;適當減小主偏角,正確刃磨鉸刀刃口;適當減小鉸孔餘量;提高鉸孔前底孔位置精度與品質或增加鉸孔餘量;選用合格鉸刀;修磨刃帶寬度;根據具體情況減少鉸刀齒數,加大容屑槽空間或採用帶刃傾角的鉸刀,使排屑順利;定期更換鉸刀,刃磨時把磨削區磨去;鉸刀在刃磨、使用及運輸過程中,應採取保護措施,避免碰傷;對已碰傷的鉸刀,應用特細的油石將碰傷的鉸刀修好,或更換鉸刀;用油石修整到合格,採用前角5°~10°的鉸刀。 |
鉸刀的使用壽命低 |
鉸刀材料不合適;鉸刀在刃磨時燒傷;切削液選擇不合適,切削液未能順利地流動切削處;鉸刀刃磨後表面粗糙度值太高。
|
根據加工材料選擇鉸刀材料,可採用硬質合金鉸刀或塗層鉸刀;嚴格控制刃磨切削用量,避免燒傷;經常根據加工材料正確選擇切削液;經常清除切屑槽內的切屑,用足夠壓力的切削液,經過精磨或研磨達到要求。 |
鉸出的孔位置精度超差 |
導向套磨損;導向套底端距工件太遠;導向套長度短、精度差;主軸軸承鬆動。
|
定期更換導向套;加長導向套,提高導向套與鉸刀間隙的配合精度;及時維修機床、調整主軸軸承間隙。 |
鉸刀刀齒崩刃 |
鉸孔餘量過大;工件材料硬度過高;切削刃擺差過大,切削負荷不均勻;鉸刀主偏角太小,使切削寬度增大;鉸深孔或盲孔時,切屑太多,又未及時清除;刃磨時刀齒已磨裂。
|
修改預加工的孔徑尺寸;降低材料硬度或改用負前角鉸刀或硬質合金鉸刀;控制擺差在合格範圍內;加大主偏角;注意及時清除切屑或採用帶刃傾角鉸刀;注意刃磨品質。
|
鉸刀柄部折斷 |
鉸孔餘量過大;鉸錐孔時,粗精鉸削餘量分配及切削用量選擇不合適;鉸刀刀齒容屑空間小,切屑堵塞。
|
修改預加工的孔徑尺寸;修改餘量分配,合理選擇切削用量;減少鉸刀齒數,加大容屑空間或將刀齒間隙磨去一齒。
|
鉸孔後孔的中心線不直 |
鉸孔前的鑽孔偏斜,特別是孔徑較小時,由於鉸刀剛性較差,不能糾正原有的彎曲度;鉸刀主偏角過大;導向不良,使鉸刀在鉸削中易偏離方向;切削部分倒錐過大;鉸刀在斷續孔中部間隙處位移;手鉸孔時,在一個方向上用力過大,迫使鉸刀向一端偏斜,破壞了鉸孔的垂直度。
|
增加擴孔或鏜孔工序校正孔;減小主偏角;調整合適的鉸刀;調換有導向部分或加長切削部分的鉸刀;注意正確操作。
|
資料來源:網路彙整
willy
19 décembre 2013
4
19
/12
/décembre
/2013
04:59
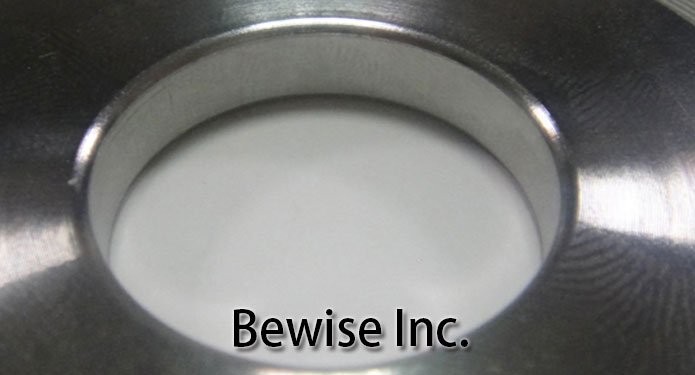
鉸孔和鑽孔、擴孔一樣都是由刀具本身的尺寸來保證被加工孔的尺寸的,但鉸孔的品9質要高得多。鉸孔餘量對鉸孔品質的影響很大,餘量太大,鉸刀的負荷大,切削刃很快被磨鈍,不易獲得光潔的加工表面,尺寸公差也不易保證;餘量太小,不能去掉上工序留下的刀痕,自然也就沒有改善孔加工品質的作用。一般粗鉸餘量取為0.35-0.15mm,精鉸取為0.15-0.05mm。鉸孔尺寸精度一般為IT9-IT7級,表面粗糙度Ra一般為3.2-0.8μm。
孔加工精度等級
加工方案 |
公差等級 |
表面粗度Ra(μm) |
適用範圍
|
鑽 |
IT13~IT11 |
20 |
加工未淬火鋼及鑄鐵的實心毛坯,也可用於加工有色金屬(表面粗糙度稍差),孔徑<(15-20)mm |
鑽-鉸 |
IT8-9 |
5.0-2.5 |
鑽-粗鉸-精鉸 |
IT7-8 |
2.5-1.25 |
鑽-擴 |
IT11 |
20-10.0 |
加工未淬火鋼及鑄鐵的實心毛坯,也可用於加工有色金屬(表面粗糙度稍差),但孔徑>(15-20)mm |
鑽-擴-鉸 |
IT8-9 |
5.0-2.5 |
鑽-擴-粗鉸-精鉸 |
IT7 |
2.5-1.25 |
鑽-擴-機鉸-手鉸 |
IT6-7 |
0.63-0.160 |
鑽-(擴)-拉 |
IT6-7 |
2.5-0.160 |
大批大量生產(精度視)除淬火鋼外各種材料,毛坯有鑄出孔或鍛出孔 |
粗鏜(或擴孔) |
IT11-13 |
20-10.0 |
粗鏜(粗擴)-半精鏜(精擴) |
IT8-9 |
5.0-2.5 |
粗鏜(擴)-半精鏜(精擴)-精鏜(鉸) |
IT7-8 |
2.5-1.25 |
粗鏜(擴)-半精鏜(精擴)-精鏜-浮動鏜刀塊精鏜 |
IT6-7 |
1.25-0.63 |
粗鏜(擴)-半精鏜-磨孔 |
IT7-8 |
1.25-0.32 |
主要用於加工淬火鋼,也可用於不淬火鋼,但不宜用於有色金屬 |
粗鏜(擴)-半精鏜-粗磨-精磨 |
IT6-7 |
0.32-0.160 |
粗鏜-半精鏜-精鏜-金剛鏜 |
IT6-7 |
0.63-0.080 |
主要用於精度要求較高的有色金屬加工 |
鑽-(擴)-粗鉸-精鉸-珩磨鑽-(擴)-拉-珩磨粗鏜-半精鏜-精鏜-珩磨 |
IT6-7 |
0.32-0.040 |
精度要求很高的孔 |
以研磨代替上述方案的珩磨 |
IT6以上 |
0.160-0.010 |
資料來源:網路彙整
willy